Presenting CliCE-DiPP Results at the iV 2025
A week ago, I had the opportunity to present our latest results from the CliCE-DiPP research project at the iV conference in Darmstadt. It was about two analysis solutions around sustainable production. One paper[1] was about the analysis of resource consumption and CO2 emissions over the entire production cycle, using a new approach based on process mining. The second paper[2] dealt with the analysis of digital product passwords in terms of CO2 emissions over their entire life cycle.
The conference was also a nice reunion with a number of former colleagues and project partners. And of course, the conference offered lots of interesting presentations on AI and visualization as well as plenty of exciting talks and technical discussions.
The International Conference on Information Visualisation (iV) is a unique platform that brings together academia, industry researchers, and societal agencies. It offers a space to share practical solutions for multidisciplinary applications with societal impacts. Beyond the research forum, it hosts the Doctoral Research Programme for PhD training and a researchers link session for collaborative research project design, providing unparalleled opportunities for learning and collaboration.
The conference theme covers Information Visualization, Visual Analytics, and AI-centred Visual Knowledge Discovery. Its structure adapts to the subject’s evolving and developments. The focus is on applying these fields that have a societal impact, such as Knowledge Visualization, Learning Analytics, and Digital Humanities Knowledge Visualization.
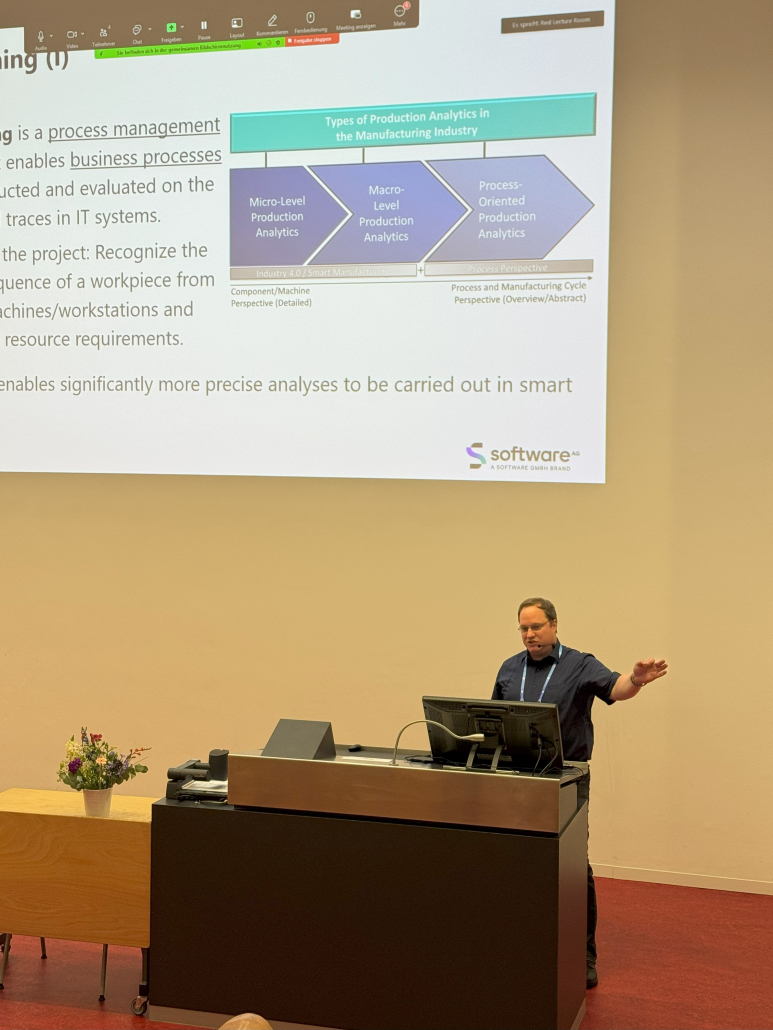
References
- (2025): Process Mining for Production Optimization in Smart Manufacturing. In: 2025 29th International Conference Information Visualisation (IV), IEEE, Forthcoming.
- (2025): DPPviewer: A Visual Analytics Approach for Optimizing Production Chains on Digital Product Passports. In: 2025 29th International Conference Information Visualisation (IV), IEEE, Forthcoming.